Discover What is Porosity in Welding and Its Effect on Architectural Stability
Unwinding the Secret of Porosity in Welding: Tips for Reducing Problems and Optimizing Quality
In the detailed world of welding, porosity continues to be a relentless obstacle that can significantly affect the top quality and stability of welded joints. As we dig into the midsts of porosity in welding, revealing the tricks to its avoidance and control will be vital for experts seeking to master the art of top quality weldments.
Understanding Porosity in Welding
Porosity in welding, an usual problem experienced by welders, refers to the presence of gas pockets or gaps in the bonded product, which can compromise the integrity and top quality of the weld. These gas pockets are normally caught during the welding procedure because of various aspects such as improper protecting gas, infected base products, or incorrect welding criteria. The development of porosity can deteriorate the weld, making it vulnerable to fracturing and rust, ultimately leading to architectural failings.
By recognizing the significance of maintaining appropriate gas securing, guaranteeing the tidiness of base materials, and optimizing welding settings, welders can substantially lower the chance of porosity formation. Generally, a detailed understanding of porosity in welding is important for welders to create high-grade and long lasting welds.
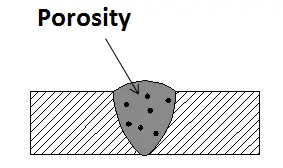
Typical Reasons For Porosity
When checking welding procedures for potential quality problems, recognizing the typical sources of porosity is necessary for keeping weld integrity and preventing structural failings. Porosity, identified by the presence of cavities or gaps in the weld metal, can considerably endanger the mechanical buildings of a welded joint. One typical source of porosity is inappropriate shielding gas coverage. Poor shielding gas circulation prices or improper gas mixtures can lead to atmospheric contamination, leading to porosity formation.
In addition, welding at inappropriate specifications, such as excessively high travel rates or currents, can generate too much turbulence in the weld pool, trapping gases and triggering porosity. By resolving these common reasons through appropriate gas securing, product prep work, and adherence to optimal welding criteria, welders can decrease porosity and boost the quality of their welds.
Techniques for Porosity Avoidance
Implementing efficient preventative procedures is critical in minimizing the incident of porosity in welding processes. One technique for porosity prevention is guaranteeing appropriate cleaning of the base steel prior to welding. Contaminants such as oil, oil, rust, and paint can bring about porosity, so comprehensive cleansing using suitable solvents or mechanical methods is vital.

Making use of high-grade filler products and securing gases that are appropriate for the base steel and welding procedure can significantly minimize the danger of porosity. Furthermore, maintaining proper welding parameters, such as voltage, current, take a trip speed, and gas flow rate, is essential for porosity avoidance.
Furthermore, employing appropriate welding methods, such as maintaining a regular traveling speed, electrode angle, and arc size, can aid protect against porosity (What is Porosity). Ample training of welders to ensure they comply with finest techniques and top quality control treatments is likewise important in minimizing porosity problems in welding
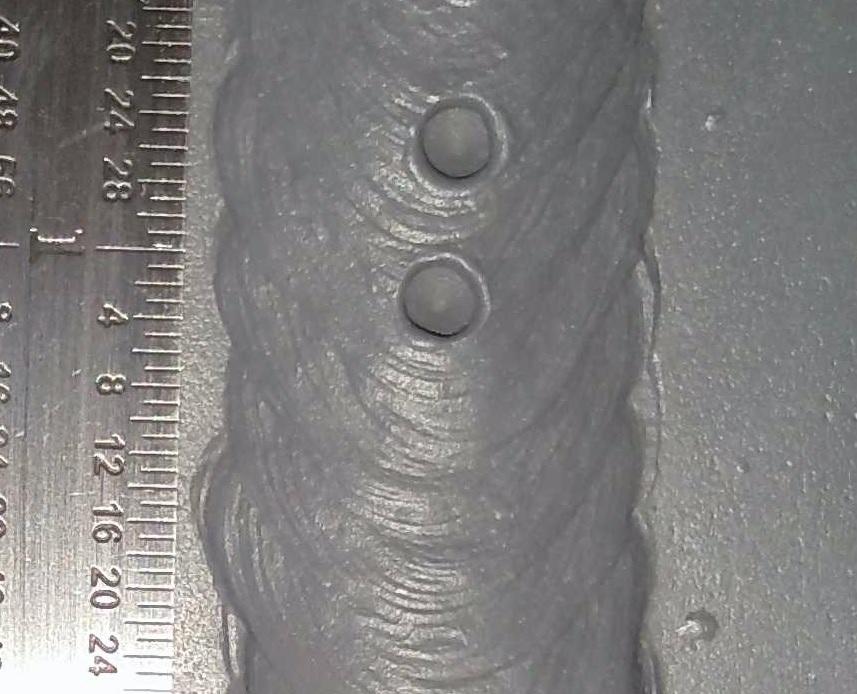
Best Practices for Top Quality Welds
Guaranteeing adherence to market standards and appropriate weld joint prep work are essential facets of attaining continually top quality welds. In enhancement to these foundational actions, there are numerous ideal practices that welders can carry out to additionally improve the top quality of their welds. One trick practice is maintaining appropriate cleanliness in the welding location. Impurities such as oil, grease, corrosion, and paint can adversely affect the high quality of the weld, bring about defects. Completely cleaning up the work surface and surrounding location before welding can assist mitigate these concerns.
Another best practice is to thoroughly select the ideal welding parameters for the specific materials being joined. Appropriate criterion choice makes certain click now optimal weld penetration, combination, and overall top quality. Making use of top notch welding consumables, such as electrodes and filler steels, can considerably influence the final weld high quality.
Value of Porosity Control
Porosity control plays an essential function in guaranteeing the integrity and quality of welding joints. Porosity, identified by the existence of cavities or spaces within the weld steel, can dramatically jeopardize the mechanical buildings and architectural honesty of the weld. Extreme porosity weakens the weld, making it more susceptible to breaking, rust, and total failure under operational tons.
Efficient porosity control is vital for maintaining the wanted mechanical homes, such as toughness, ductility, and sturdiness, of the bonded joint. What is Porosity. By minimizing porosity, welders can enhance the overall high quality and integrity of the weld, guaranteeing that it fulfills the efficiency needs of the intended application
Moreover, porosity control is crucial for attaining the preferred visual look of the weld. Extreme porosity not just weakens the weld but likewise interferes with its aesthetic appeal, which can be essential in sectors where aesthetic appeals are important. Correct porosity control methods, such as making use of the right shielding gas, managing the welding parameters, and making certain appropriate tidiness of the base products, are necessary for generating top notch welds with very little issues.
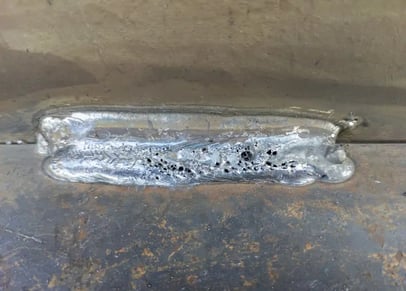
Final Thought
Finally, porosity in welding is a typical problem that can endanger view the top quality of the weld. By understanding the sources of porosity and executing proper avoidance strategies, welders can lessen directory flaws and accomplish higher quality welds. It is necessary to control porosity in welding to guarantee the stability and strength of the end product. Executing finest practices for porosity control is critical for accomplishing optimum welding results.